Products/Solutions
The Centerpiece of a Touchless™ Monitoring Solution - The DVS3000 Substation Hardened Digital Video Server
September 12, 2024
Electric utilities have long relied on physical inspections and scheduled maintenance programs when managing grid infrastructure. However, the periodic nature of these approaches allows potential faults to go undetected, sometimes for months at a time. This increases the likelihood of a catastrophic equipment failure that results in an outage and requires an emergency repair.
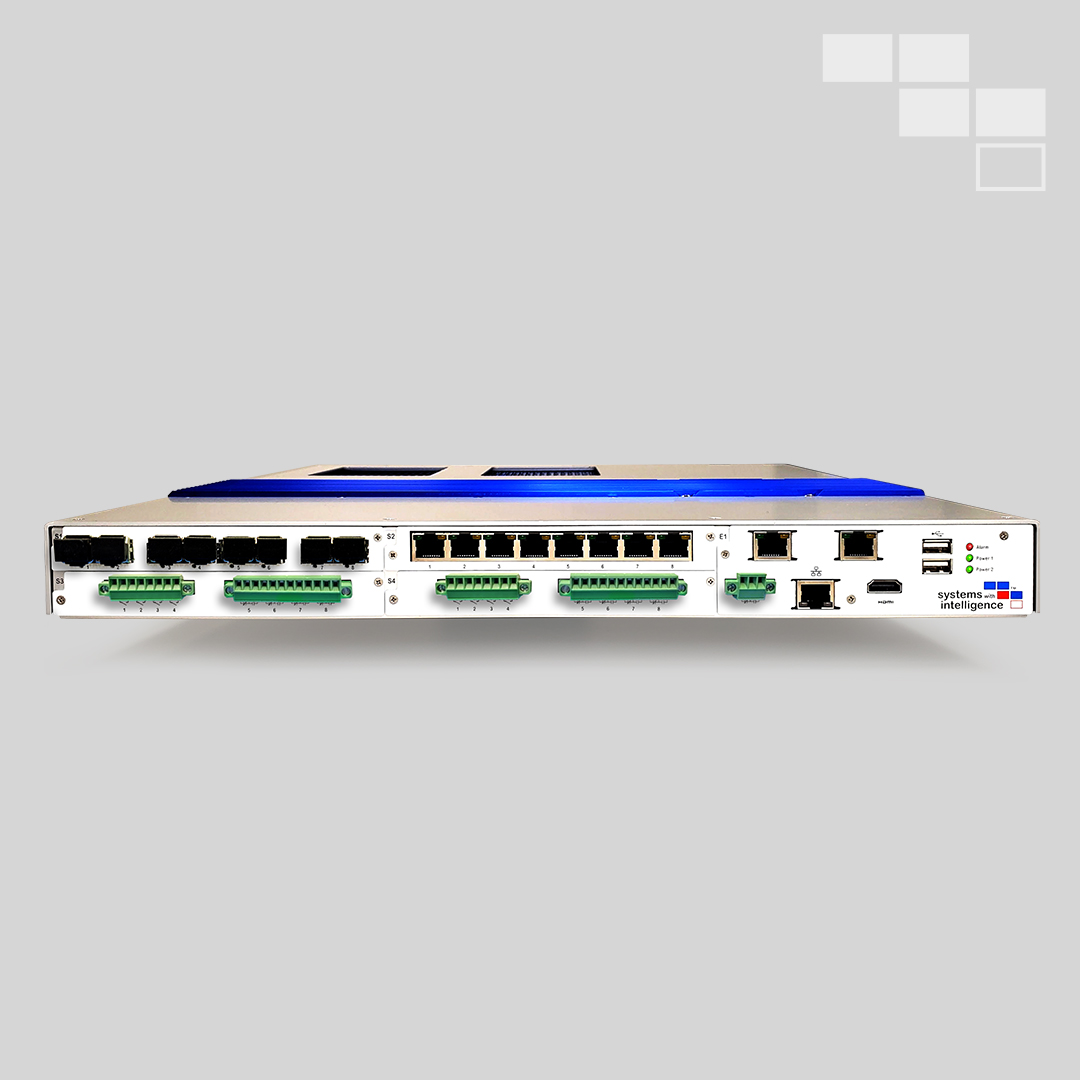
Moving Away From Physical Inspections - How Downstream Oil Refineries Can Use Thermal & Visual Monitoring Solutions
June 7, 2024
A downstream oil refinery processes hundreds of thousands of barrels of crude oil each day before storing the various products and distributing them to customers. The refinery takes maintenance seriously, creating maintenance schedules for each asset and conducting regular physical inspections beyond what is required to comply with regulations.
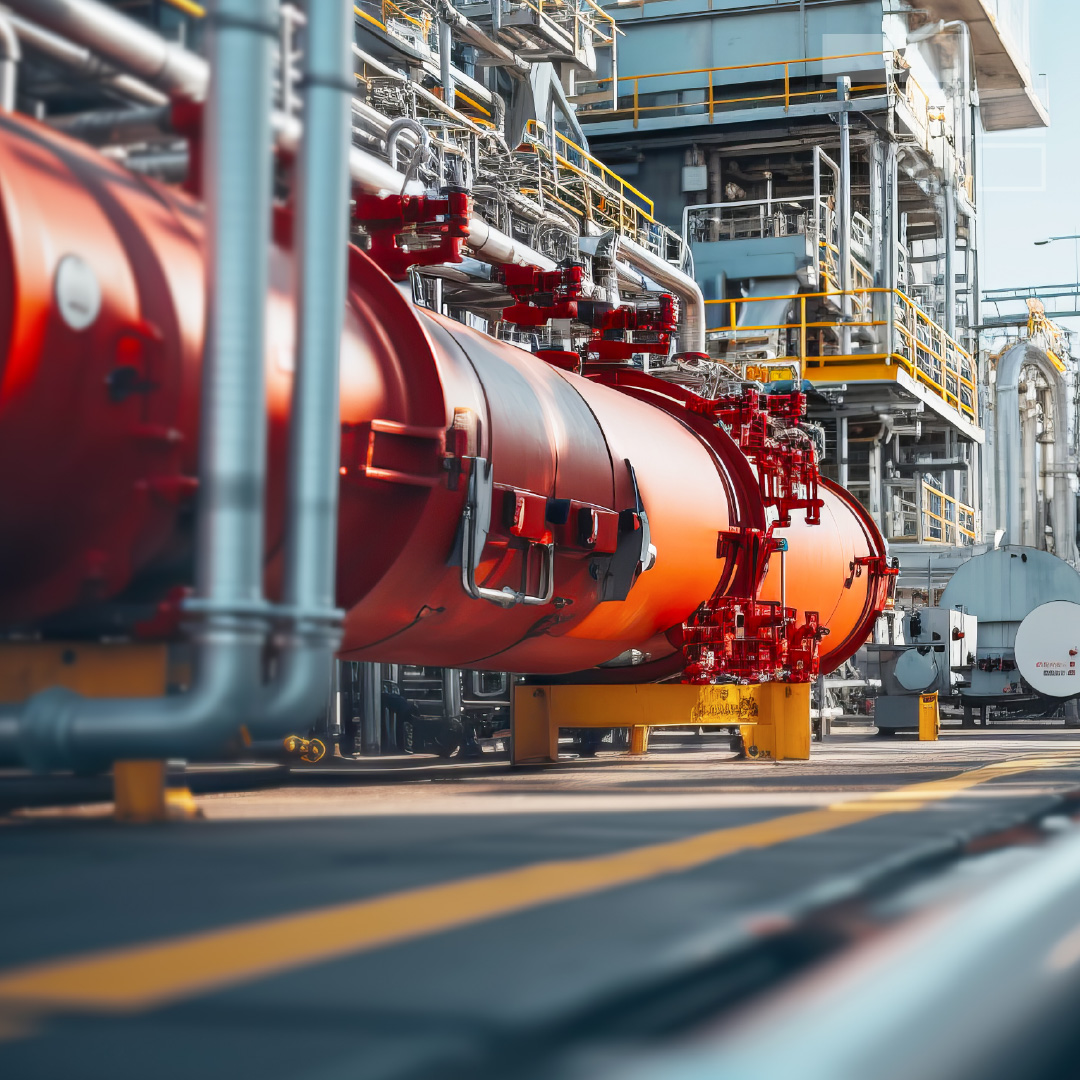
Bulk Tank Gauging and Measurement for Midstream Oil Processing and Storage
October 25, 2024
The Scenario - Bulk Storage Tank Levelling and Gauging A midstream oil processing and storage company operates numerous bulk storage terminals across a large geographical area. Product sent through pipelines from upstream oil exploration and production companies arrives at the site for storage, processing, and transporting onward to downstream refineries.
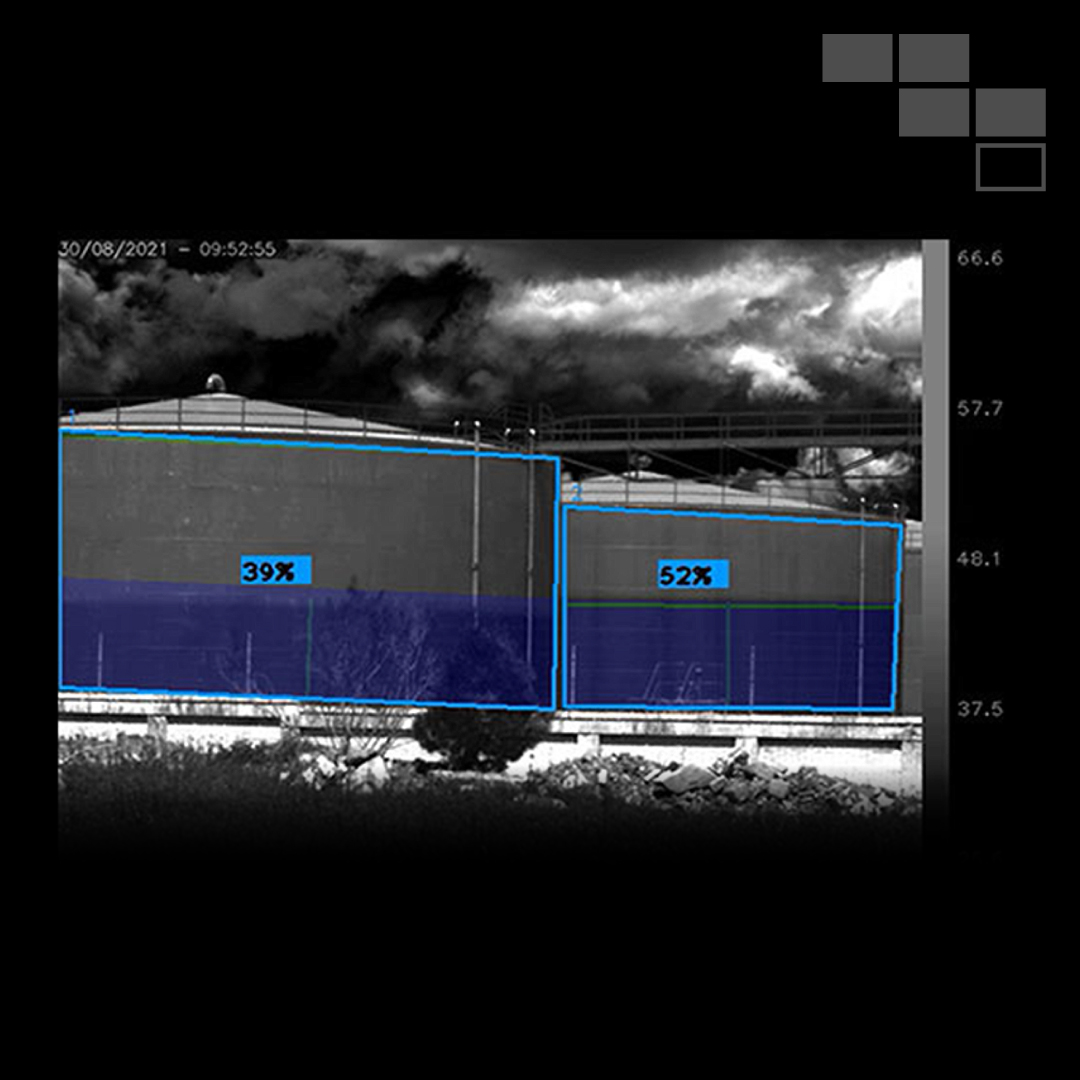
Leak Detection & Repair - Reducing Emissions and Lost Product From Oil Wells
June 7, 2024
The Scenario - Undetected Leaks at Remote Oil Wells
A mid-sized oil exploration and production company operates numerous oil wells across a wide geographic area. To comply with regulations, the company conducts periodic physical inspections using handheld sensors and other manual leak detection techniques. Many of these wells are remote and difficult to access, increasing the time and cost required to dispatch a crew and conduct the inspection.
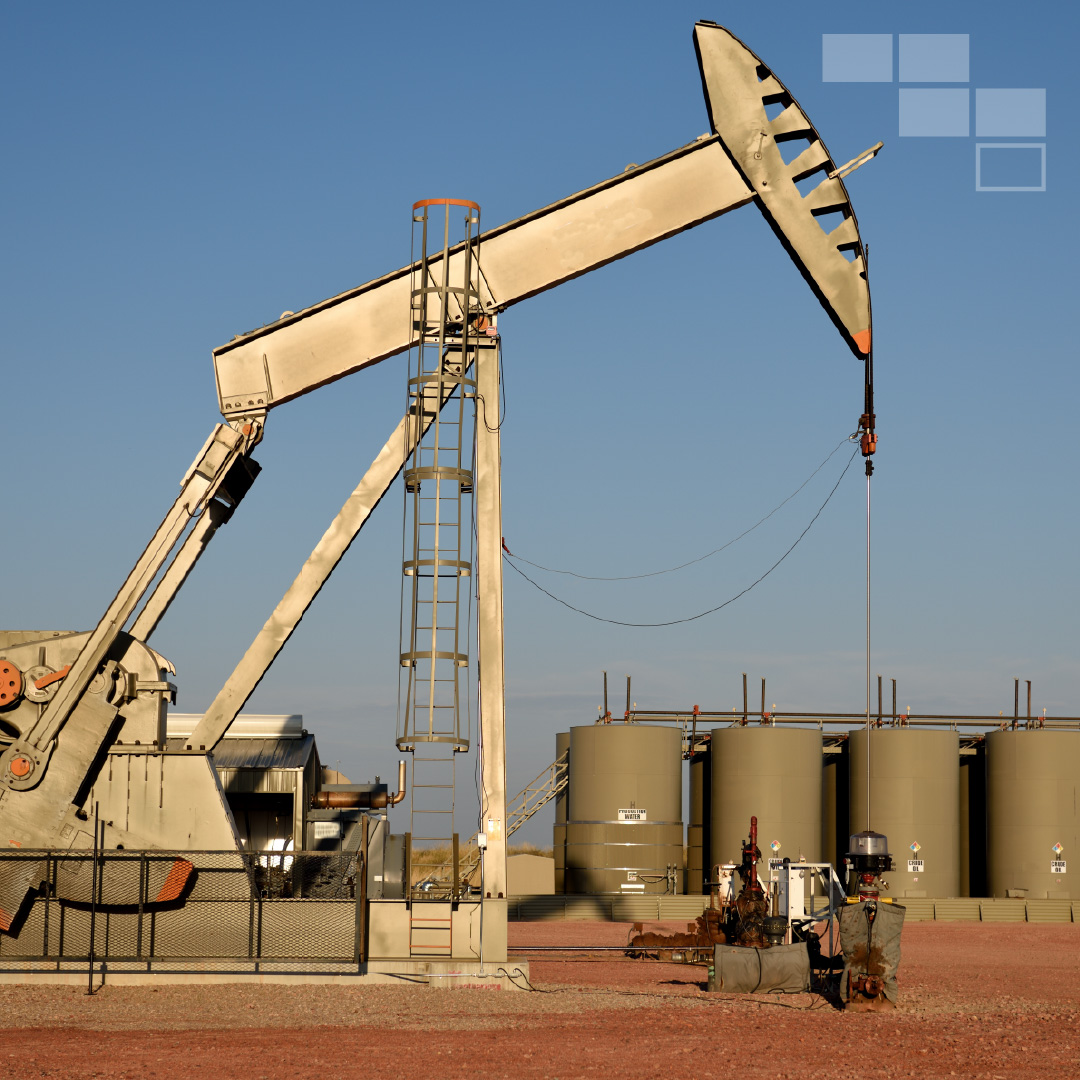
Reducing Fugitive Emissions - The Role of Touchless™ Monitoring for Leak Detection and Repair in Oil & Gas
February 22, 2024
The oil & gas industry contributes a significant share of total greenhouse gas (GHG) emissions. Much of these emissions are in the form of methane, a highly potent but short-lived GHG that is responsible for as much as 30 percent of the rise in global temperatures.
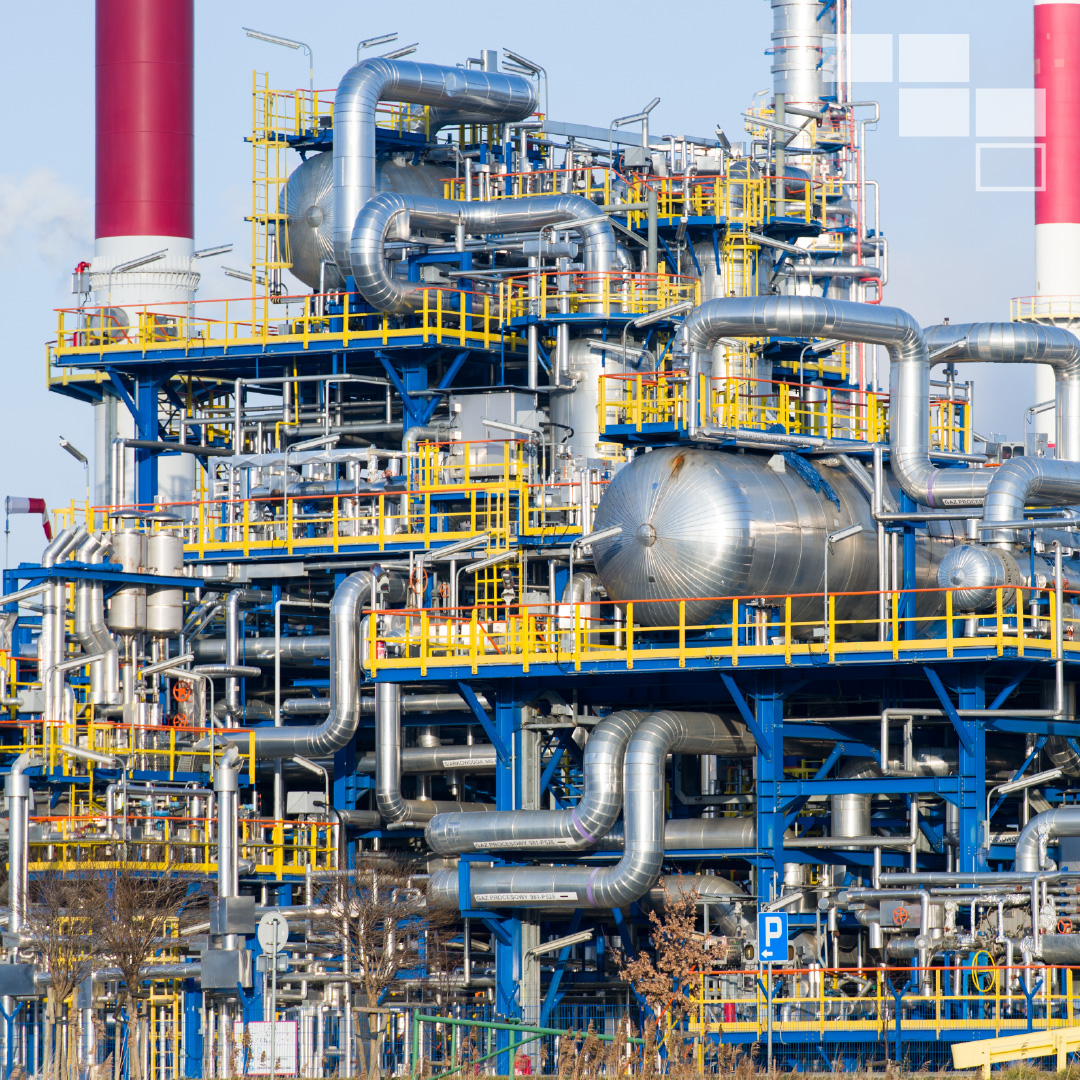
Using Touchless™ Monitoring For Oil and Gas - The Upstream, Midstream, and Downstream Applications of Thermal and Visual Sensors
February 22, 2024
The oil & gas industry faces increasing public, investor, and regulatory pressure to reduce greenhouse gas (GHG) emissions, improve workplace safety, and mitigate the environmental impact of activities across the production process.
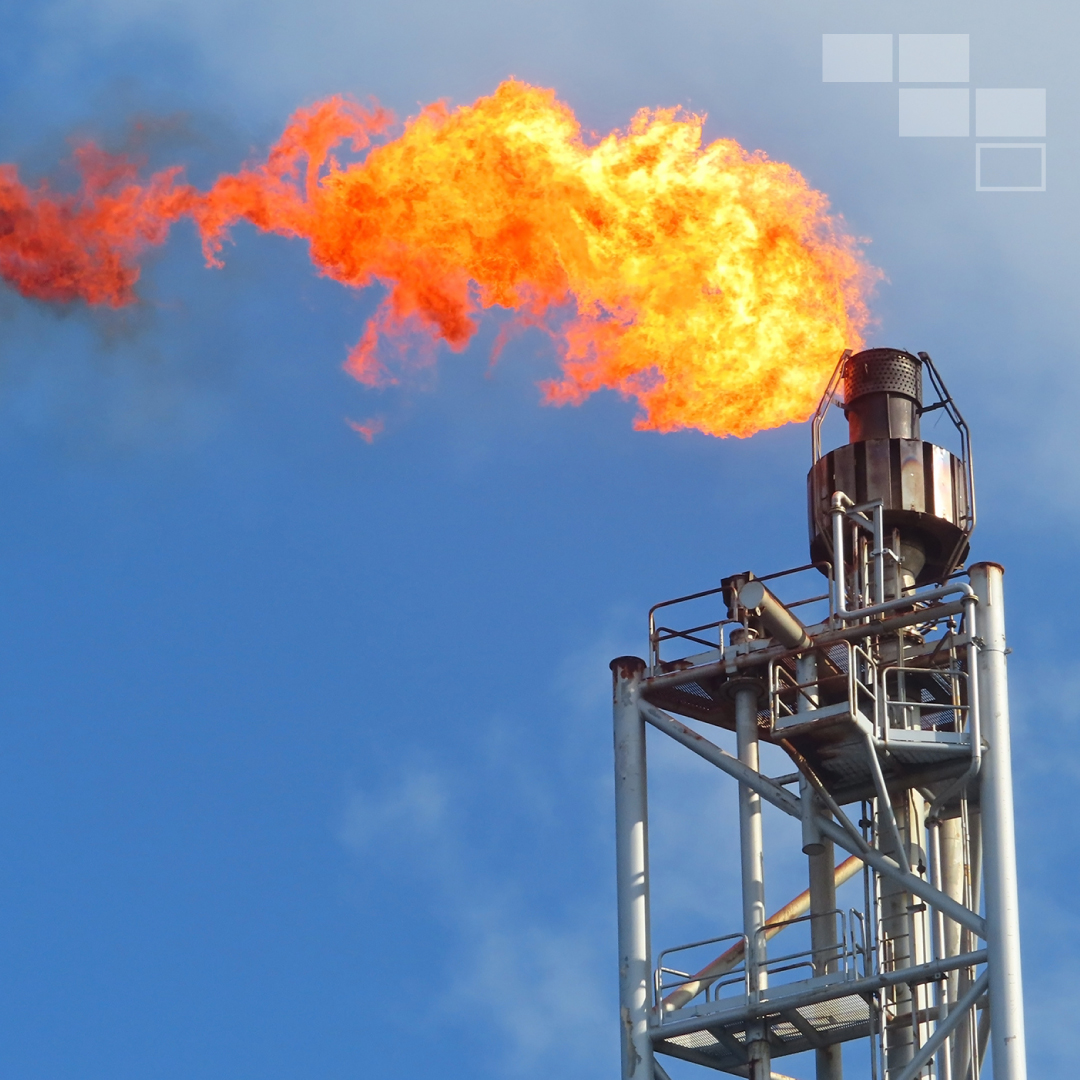
Case Study: Learn why Iberdrola Australia Chose Systems With Intelligence Touchless™ Monitoring
August 16, 2024
Iberdrola Australia is a leading renewable energy provider that generates and contracts electricity from wind turbines, solar photovoltaic, and other low-emission energy sources. With over 1,100 MW of installed capacity and more than 2,500 MW of planned capacity, the company provides clean and sustainable electricity to individuals, households and businesses throughout Australia.
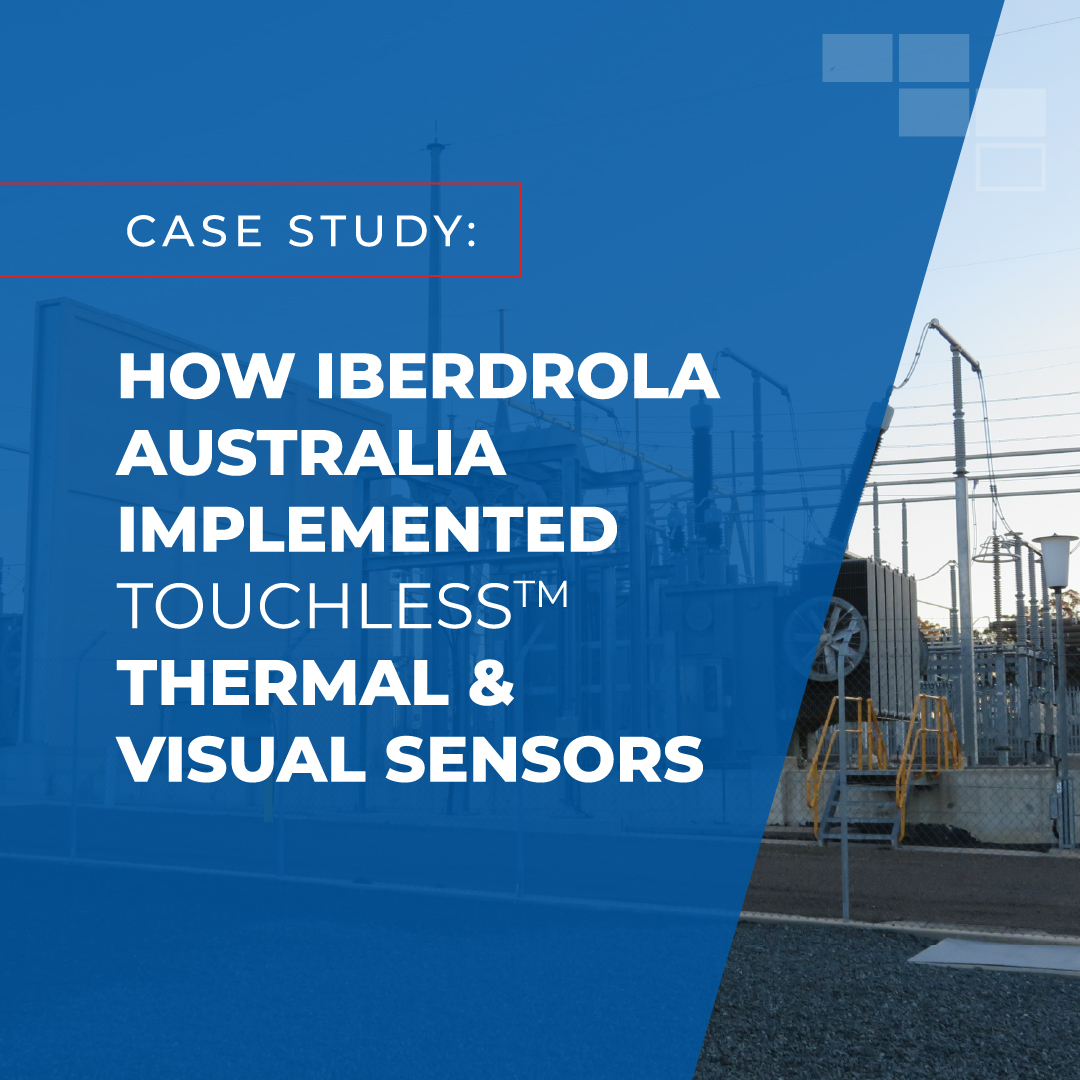
4 Benefits of Touchless™ Monitoring Solutions for the Oil & Gas Industry
August 9, 2024
The oil & gas industry has long used cameras for security and safety applications. In case of an incident, teams could review the video footage and see what happened. But they had limited capabilities to actually prevent an issue from occurring in the first place. Today, Touchless™ Monitoring solutions allow data from thermal and visual sensors to be used proactively, not just reactively. The explosion-proof sensors provide 24/7 continuous monitoring of upstream, midstream, or downstream facilities for a wide range of applications.
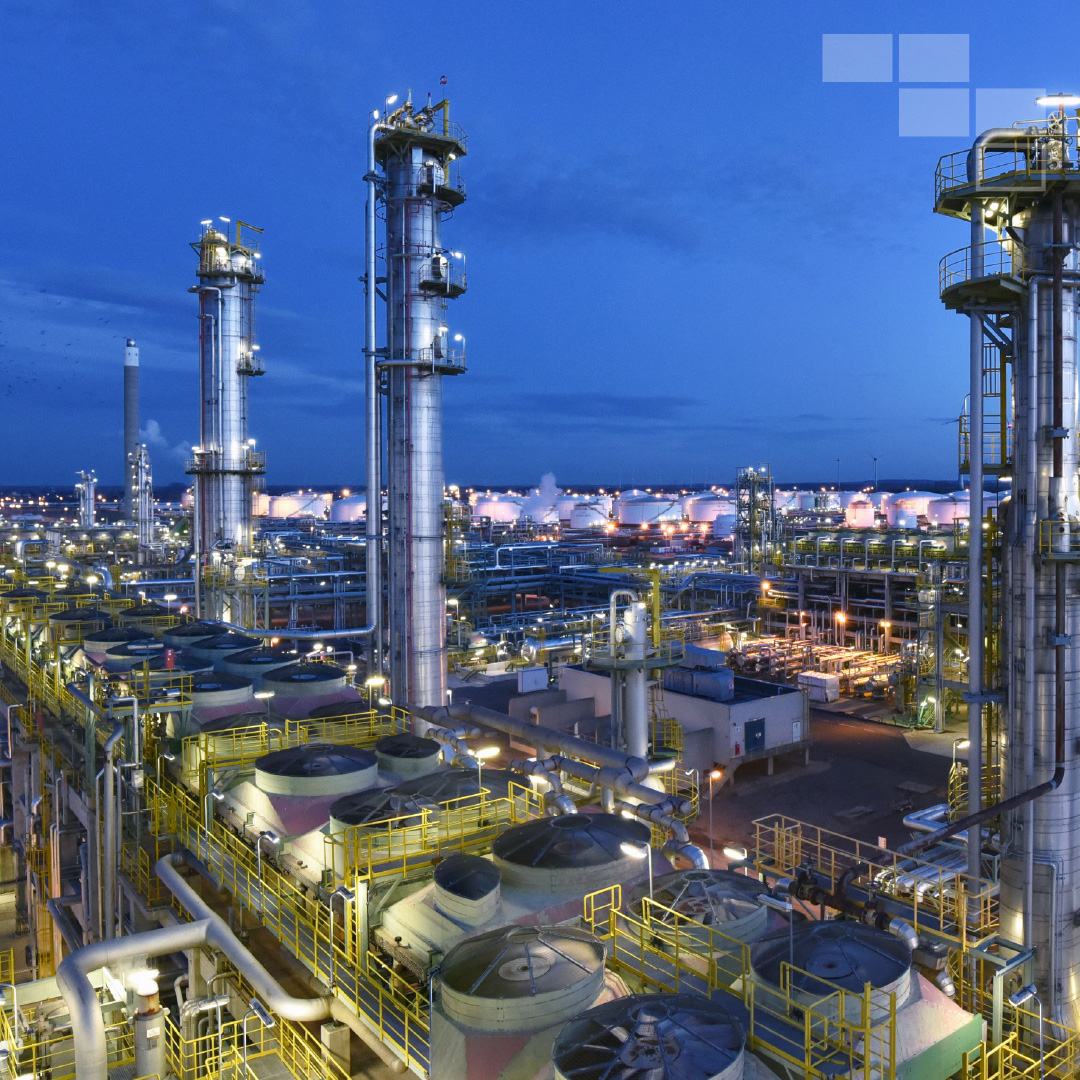
Improving Operations & Maintenance With Touchless™ Monitoring for Oil & Gas Facilities
June 7, 2024
The oil & gas industry plays a significant role in the North American economy. As global energy demand recovers, the North American oil & gas market is expected to grow to more than $356 billion by 2025. Extracting, transporting, refining, and distributing oil & gas requires a complex mix of diverse and geographically dispersed facilities. Each of these sites faces unique challenges, especially when it comes to the operation and maintenance of high-value industrial assets.
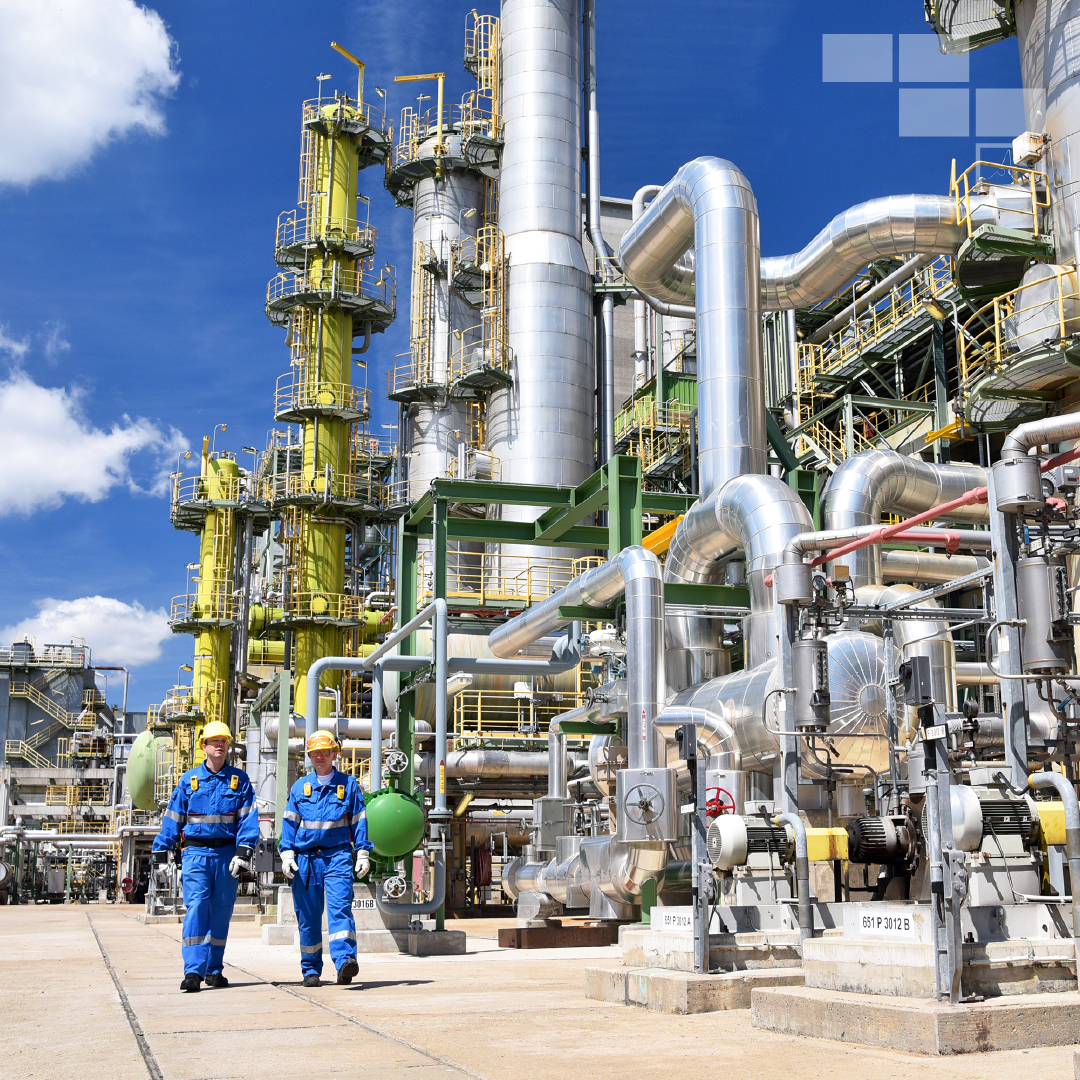
From Pilot to Rollout - Scaling Up Remote Substation Monitoring Solutions
August 16, 2024
Thermal and visual sensors are familiar technology for utilities. Technicians already leverage similar tools when conducting physical inspections at remote substations, and the data provided by these sensors allows utilities to identify potential issues and schedule repairs.
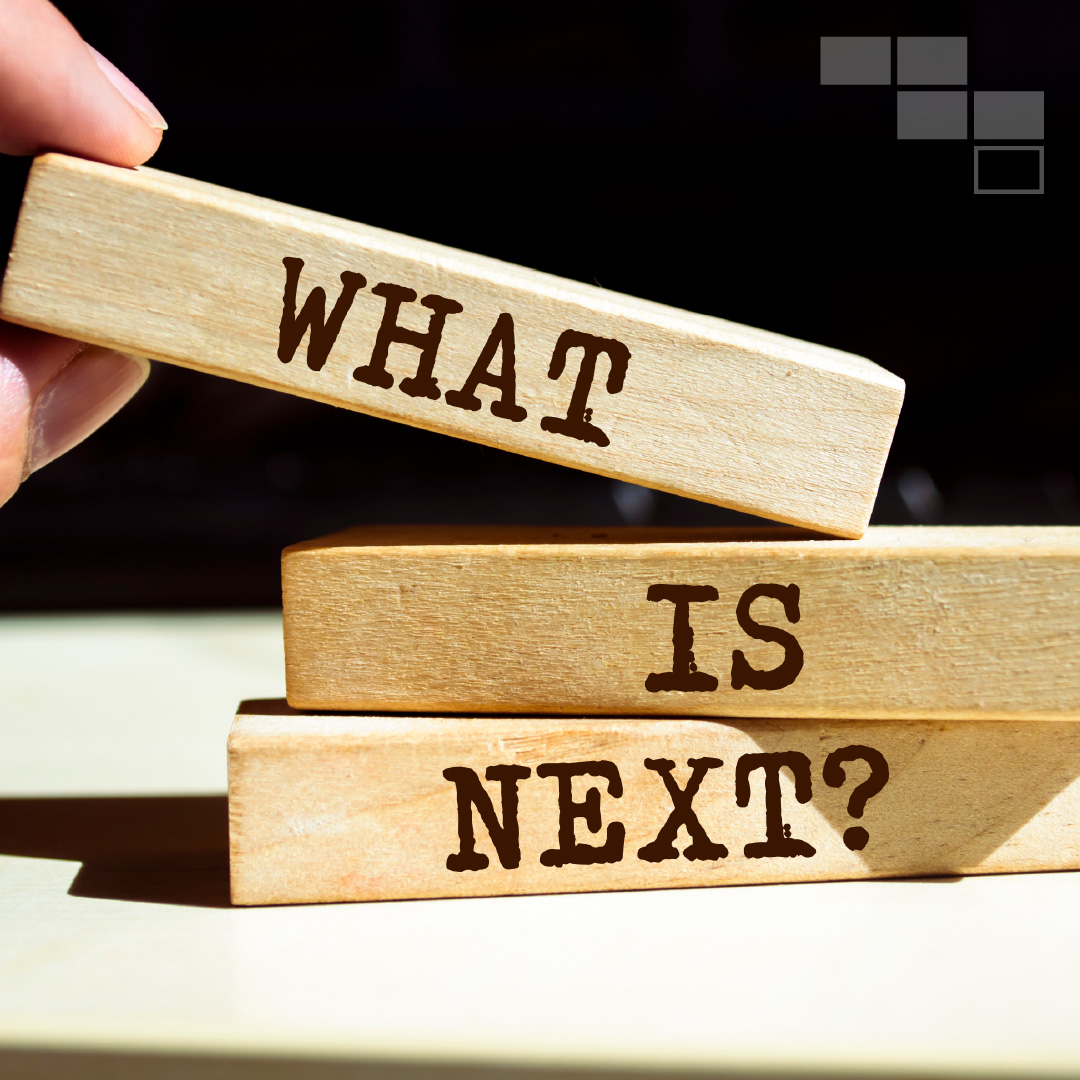
Reducing Substation Maintenance Costs With Utility-Grade Thermal and Visual Sensors
August 13, 2024
A midsized utility operates numerous remote electrical substations distributed across a wide geographic region. Physical inspections are conducted on a periodic, scheduled basis using handheld thermal scanners and other equipment to determine the health of substation assets, diagnose issues, and prioritize repairs.
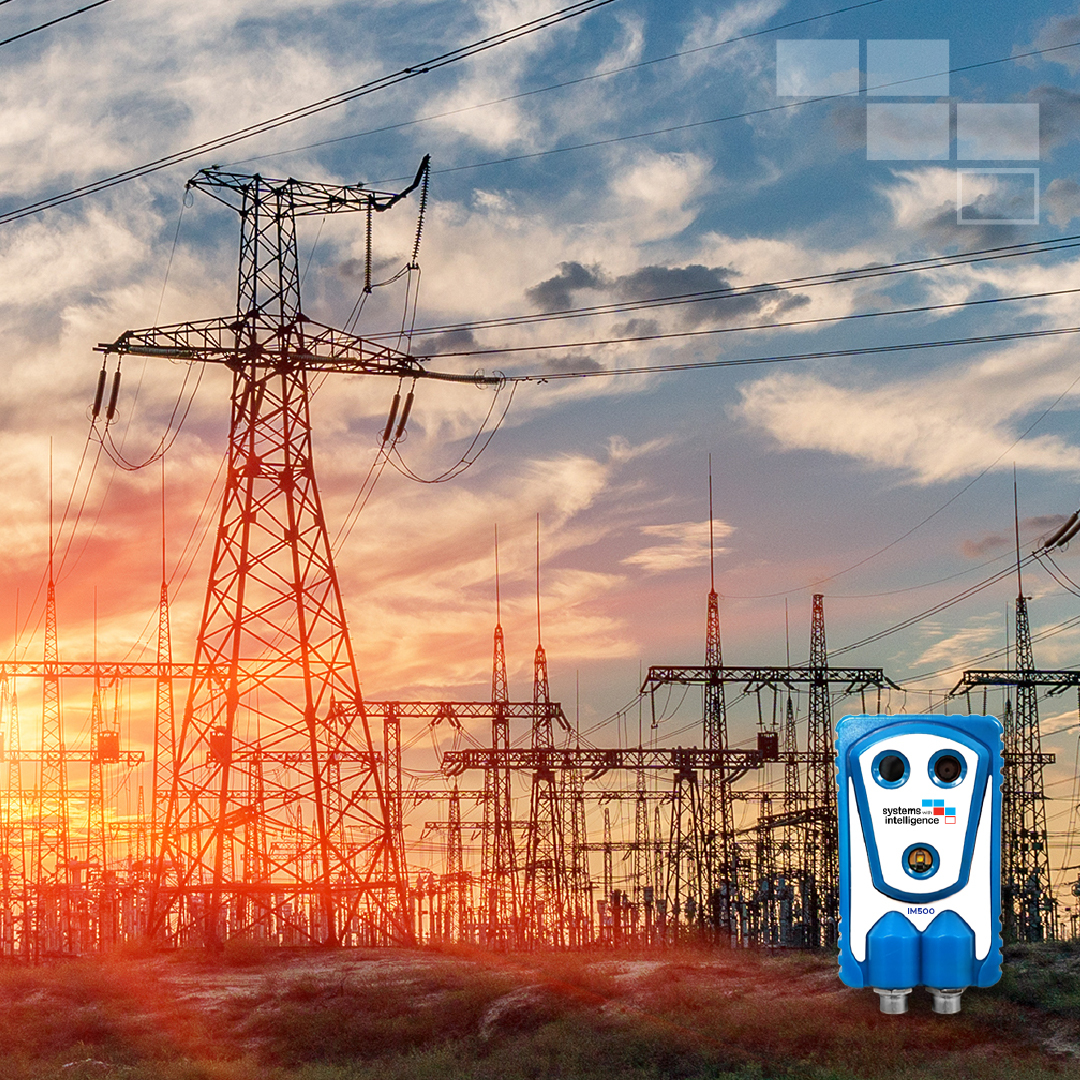
3 Reasons Utilities Should Embrace Automated Thermal Imaging for Remote Substation Monitoring
August 16, 2024
Electrical utilities play a vital role in delivering safe and reliable power to consumers, businesses, and governments. In the U.S. alone, more than $400 billion of electricity flows through more than 7 million miles of high voltage transmission and distribution lines that criss-cross the country. More than 55,000 substations convert that voltage to distribution levels so that it can be safely used.
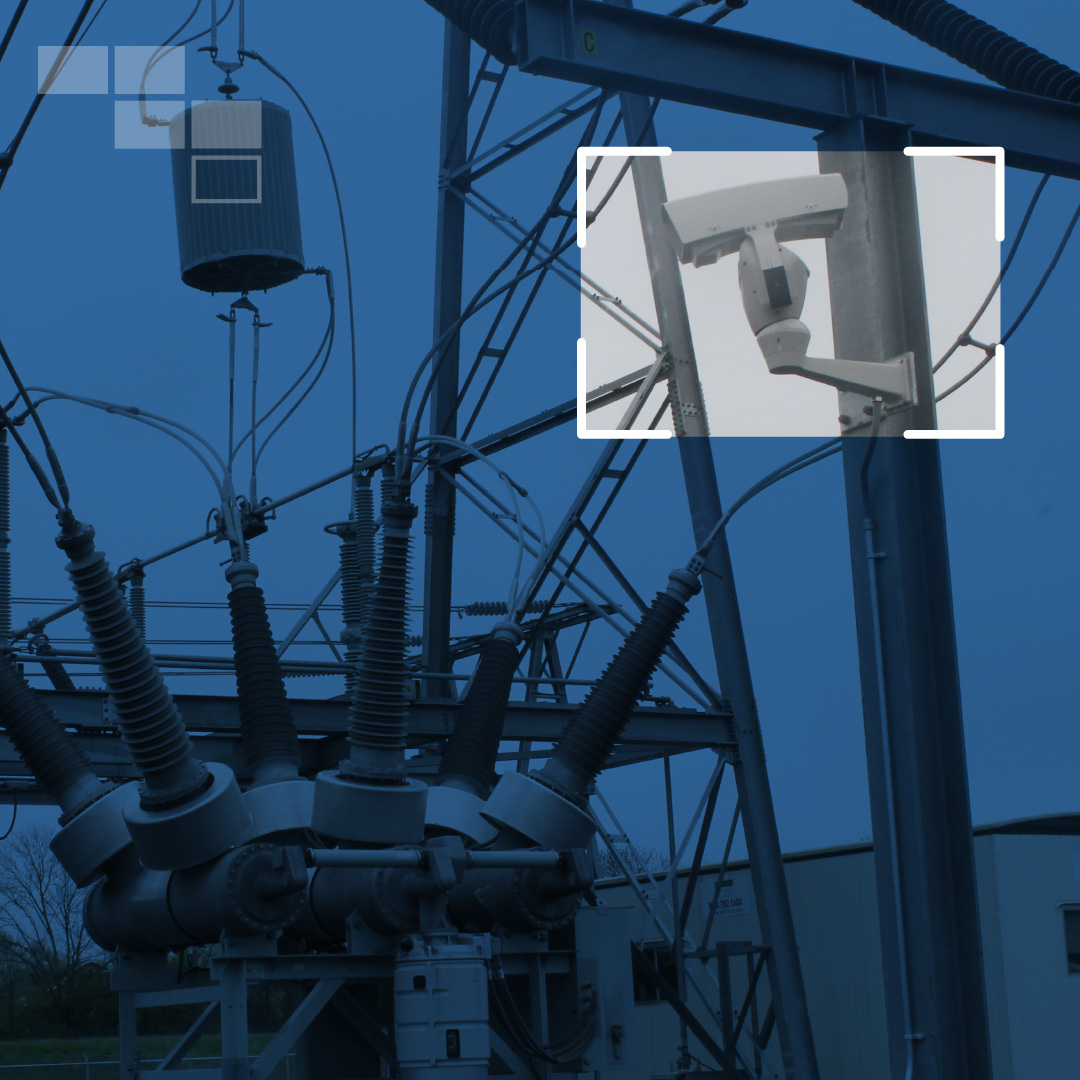
The Calm After the Storm – How Utilities Can Inspect Assets With the TCAM2500 Sensor
August 13, 2024
After a major storm, electrical utilities must rapidly diagnose and repair damage to critical infrastructure to restore power and mitigate the effects of large-scale outages. With trees down, roads flooded, and traffic at a standstill, it is often difficult for maintenance and repair crews to travel to remote substations to conduct physical inspections. Because they lack visibility ahead of time, , they may drive to the remote site and discover little or no damage, that they lack a part required to conduct a repair, or that they cannot access it due to safety concerns.
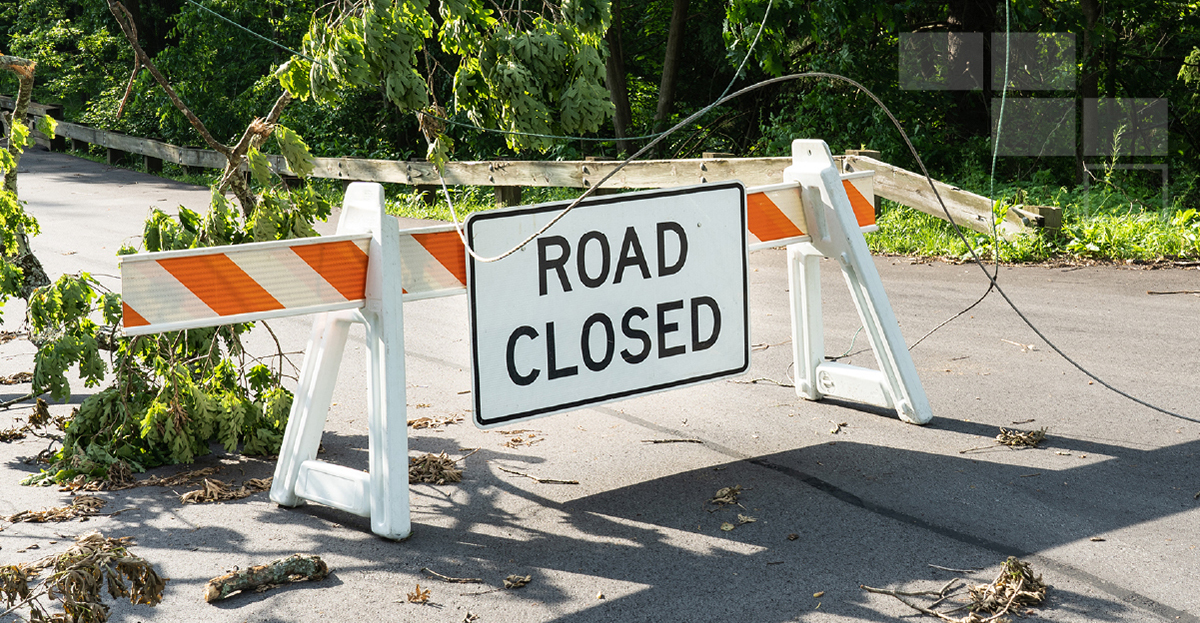
Maintaining Remote Substations – Four Challenges Utilities Can Overcome With Touchless™ Monitoring
August 13, 2024
Utility substations play a vital role in the transmission and distribution of electricity to customers, businesses, and communities. However, keeping these substations up and running can be challenging, especially when they are in remote locations far from other infrastructure.
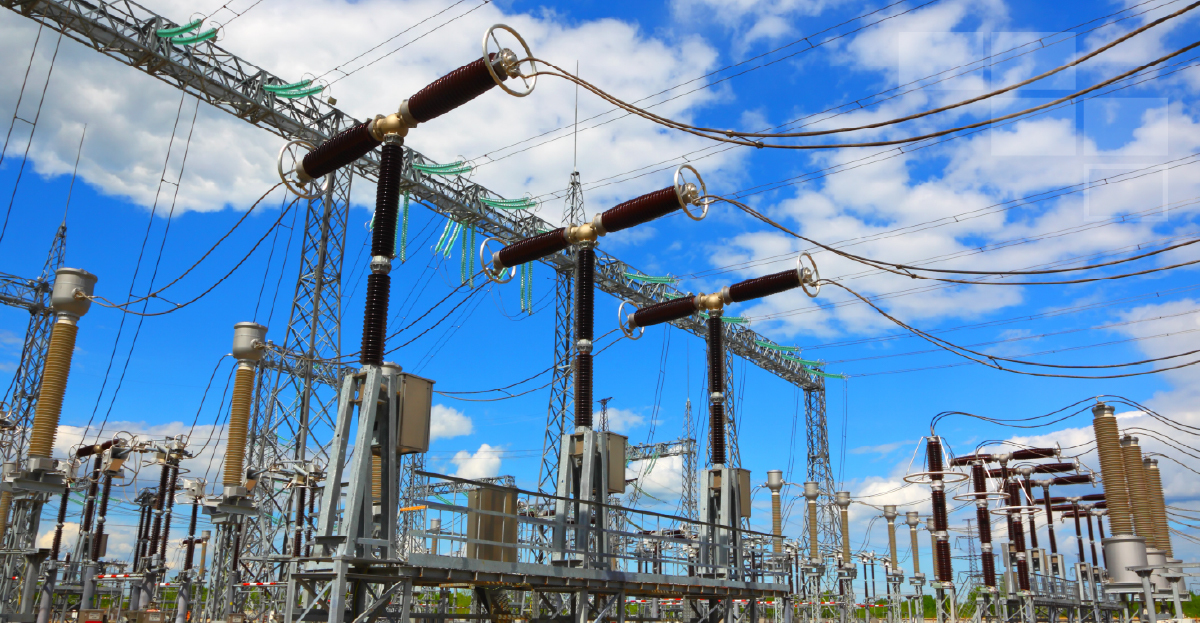
Data, Not Truck Rolls – Using the IM500 Thermal & Visual Sensor for Substation Monitoring
August 16, 2024
The Operations group at a midsized electrical utility is responsible for monitoring and maintaining numerous remote substations across a wide geographic region. As the substation infrastructure ages and demand for reliable power generation grows, maintenance and repair crews are under increasing pressure to avoid outages and ensure the system is fully functional.
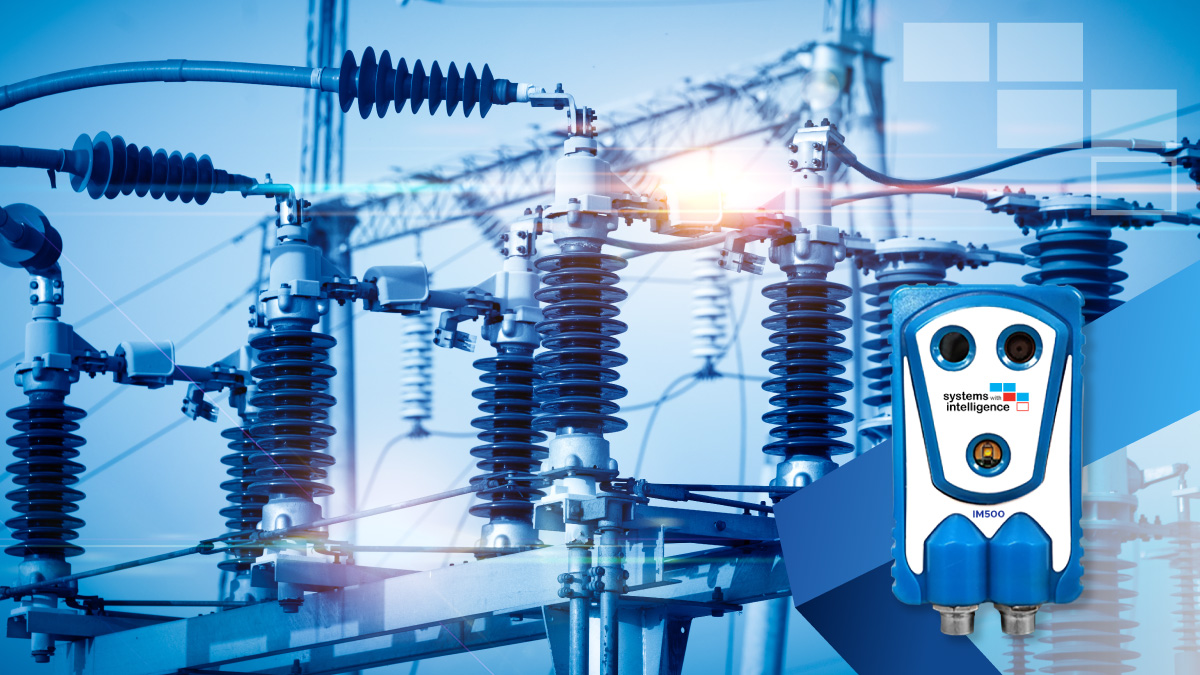
Shifting to Condition Based Maintenance With the TCAM2500 Thermal & Visual Monitoring System
August 13, 2024
The Operations group at an electric power utility is struggling to manage and maintain equipment at large remote substations. Aging infrastructure, a lack of automation systems, and a shortage of qualified staff have increased the frequency and severity of unplanned outages resulting in fines and higher maintenance costs. As issues occur, crews are dispatched reactively to physically inspect the site, identify the cause, and conduct repairs.
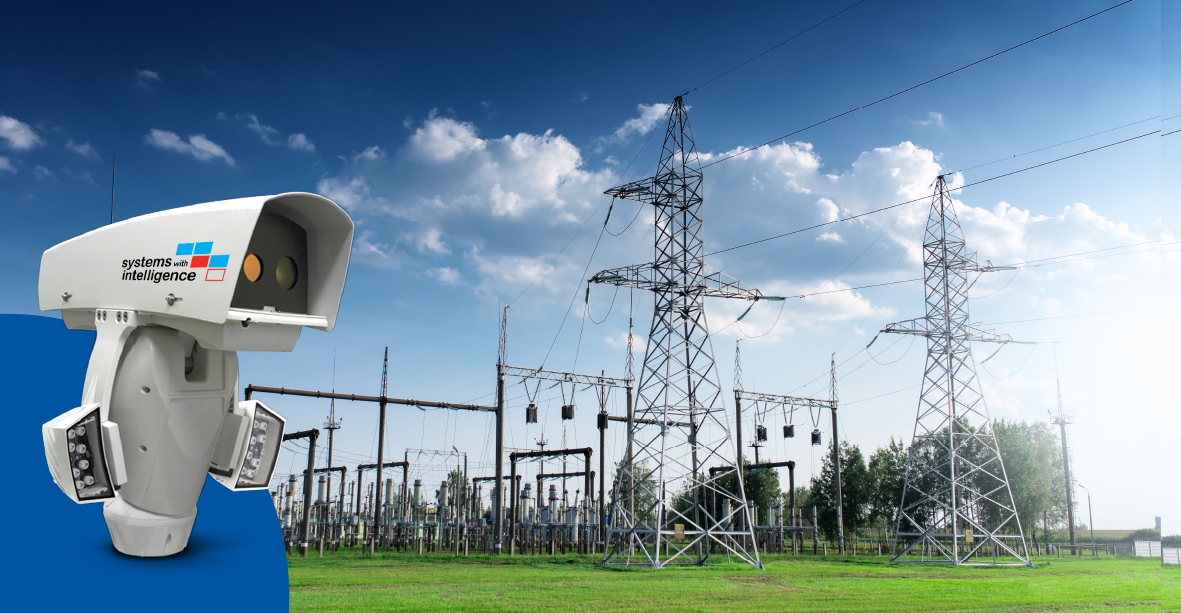